In the dynamic realm of metrology, where precision is paramount, manual measuring instruments play a crucial role in obtaining accurate and reliable measurements. From calipers and micrometers to depth gauges and dial indicators, the proficiency in utilizing these tools is central to ensuring the quality and integrity of various engineering, manufacturing, and scientific processes.
Stable Setup: Establishing a stable setup involves not only selecting a flat and sturdy surface but also considering factors like minimizing vibrations in the surrounding environment. Utilize anti-vibration pads or isolation mounts to further enhance the stability of the work area. This meticulous attention to setup details is essential, especially in precision industries where even the slightest movement can introduce errors.
Proper Calibration: Beyond the regularity of calibration, delve into the calibration process itself. Employ advanced calibration techniques such as multi-point calibration to account for potential non-linearities in the instrument's response. Explore the use of traceable calibration standards to anchor the instrument's accuracy to recognized measurement references, thereby instilling a higher level of confidence in the calibration process.
Correct Technique: Drill down into the specifics of correct technique. Implement standardized training programs that include practical exercises on proper instrument handling. Emphasize the intricacies of maintaining a consistent measuring force, ensuring that operators not only understand the theoretical aspects but can also execute precise techniques in real-world applications.
Lighting Conditions: Optimize lighting conditions by incorporating adjustable light sources or task lighting. Consider the use of LED illumination with color temperature control to achieve the most favorable conditions for different materials and surface finishes. Integrating smart lighting systems that automatically adjust to the specific requirements of the measuring task can further enhance the overall visibility and accuracy of readings.
Parallax Correction: Provide in-depth training on parallax correction techniques. Incorporate practical exercises that simulate scenarios where parallax errors may occur, allowing operators to develop a keen eye for its detection and correction. Utilize visual aids or augmented reality overlays that guide operators in aligning their line of sight with the measurement markings, thereby mitigating parallax-related inaccuracies.
Zero Point Adjustment: Explore advanced zero point adjustment methods, such as dynamic zeroing that compensates for drift during measurements. Implement automated zero-setting features in instruments where applicable, reducing reliance on operator intervention and minimizing the chances of oversights. Integrate real-time feedback systems that alert operators if zero calibration is required, ensuring proactive correction.
Repeat Measurements: Take repetition to the next level by implementing statistical analysis of repeated measurements. Introduce concepts such as standard deviation and confidence intervals to quantify the reliability of the measured values. Incorporate automated measurement systems that can execute multiple measurements rapidly, enabling a more extensive dataset for robust statistical analysis.
Record Units: Extend the emphasis on recording units by standardizing units across the organization. Implement digital recording systems that automatically convert measurements into standardized units, reducing the likelihood of manual input errors. Consider adopting the International System of Units (SI) as a universal standard, promoting consistency in documentation across global projects and collaborations.
Document Environmental Conditions: Develop a comprehensive environmental monitoring system that continuously records and logs conditions during measurements. Integrate sensors that capture not only temperature and humidity but also factors like air pressure and air quality. This wealth of environmental data serves not only as a reference for measurement accuracy but also as a resource for analyzing the impact of environmental variables on specific materials and measurement processes.
Stainless steel corked- backed ruler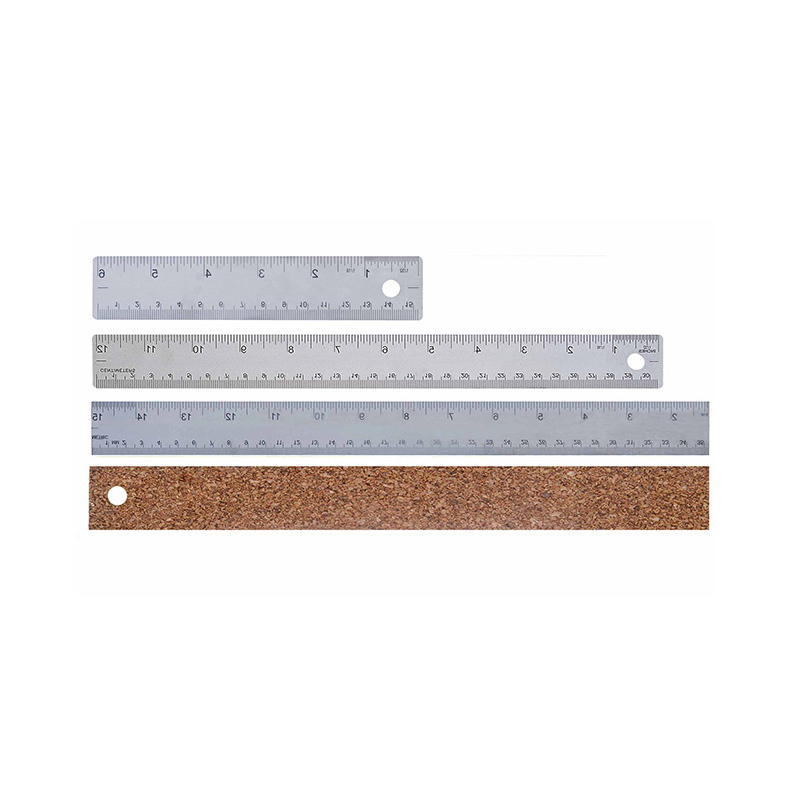