Common error sources in digital caliper measurements can arise from various factors, and it's essential to understand and address them to ensure accurate results. Here are some common error sources and ways to minimize or correct them:
Calibration Issues:
Problem: Digital calipers necessitate periodic calibration to sustain accuracy, as deviations from the calibrated state can introduce errors.
Solution: Establish a robust calibration schedule based on the manufacturer's recommendations. Utilize certified calibration standards with traceability to national or international standards. Document calibration procedures and results meticulously for stringent quality control.
Battery Issues:
Problem: Low battery levels can adversely impact the stability of electronic components, resulting in inaccurate measurements.
Solution: Implement a proactive battery replacement program, strictly adhering to the manufacturer's guidelines. Contemplate the use of rechargeable batteries and vigilantly monitor the low-battery indicator on the caliper. Maintain a ready supply of fresh batteries to minimize downtime and uphold measurement accuracy.
Environmental Conditions:
Problem: Fluctuations in temperature, humidity, and exposure to dust can jeopardize the integrity of both mechanical and electronic components in the digital caliper.
Solution: Operate the caliper within the manufacturer-specified temperature and humidity range. Enforce stringent storage practices and protective measures to shield the caliper from environmental contaminants when not in use.
Mechanical Wear:
Problem: Regular usage can inevitably lead to wear on the caliper's moving parts, potentially compromising precision.
Solution: Institute a systematic maintenance schedule involving thorough inspection and lubrication of moving parts. Adhere strictly to the manufacturer's guidelines for maintenance procedures. Promptly replace worn components to sustain the caliper's accuracy over time.
Parallax Error:
Problem: Misalignment of the user's line of sight with the scale can introduce parallax error, particularly in traditional calipers.
Solution: Train users rigorously to position their eyes perpendicular to the scale, minimizing parallax. Alternatively, consider the adoption of digital calipers with a digital readout, substantially mitigating parallax errors associated with analog scales.
Material Expansion/Contraction:
Problem: Variations in material dimensions due to temperature changes may significantly impact measurement accuracy.
Solution: Allow materials to acclimate to the measurement environment before readings. Alternatively, opt for temperature-compensated calipers designed to offset the effects of temperature changes on measurements.
Digital Display Glitches:
Problem: Malfunctions in the digital display can lead to erroneous readings, potentially compromising the reliability of measurements.
Solution: Vigilantly inspect the digital display for anomalies and artifacts at regular intervals. If persistent issues arise, seek assistance from the manufacturer's support or service center for thorough diagnosis and resolution.
Electronic Interference:
Problem: External electromagnetic interference poses a threat to the integrity of digital signals within the caliper.
Solution: Use the caliper away from potential sources of electromagnetic interference. Contemplate the adoption of models equipped with shielding or filtering mechanisms to minimize the adverse impact of electronic interference on measurements.
Zero-Point Drift:
Problem: The zero point (tare) may exhibit drift over time, potentially leading to inaccuracies in measurements.
Solution: Implement a meticulous zero-point calibration procedure. Regularly reset the zero point and recalibrate the caliper, particularly following exposure to extreme conditions or intensive use, to ensure sustained accuracy in measurements.
Digital caliper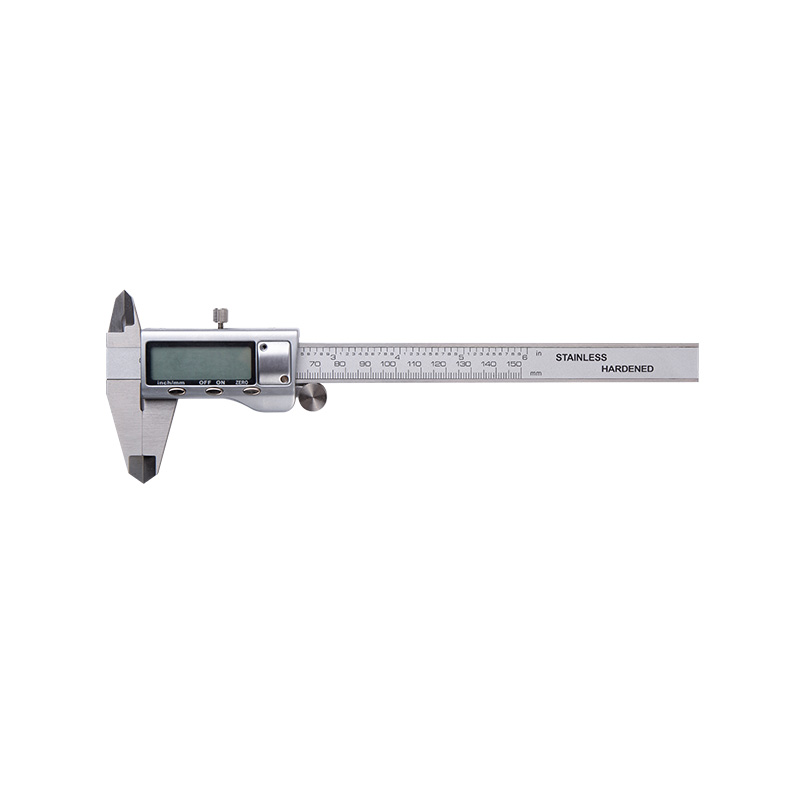