Manual measuring tools maintain precision and repeatability through several mechanisms and considerations:
High-Quality Construction: The construction of manual measuring tools is a meticulous process that begins with the selection of materials known for their superior properties. High-grade alloys, precision-machined components, and advanced polymers are chosen to ensure both durability and dimensional stability. Each tool undergoes stringent manufacturing processes, including CNC machining and surface treatments, to eliminate imperfections and achieve the highest level of mechanical integrity. Quality control measures at every step of the production process guarantee that the final product meets exacting standards.
Calibration: Calibration is a sophisticated operation involving state-of-the-art equipment and highly skilled technicians. Precision laboratories with controlled environmental conditions are employed to conduct thorough calibration procedures. These procedures go beyond a simple comparison with standards; they involve statistical analyses, uncertainty assessments, and traceability to national or international standards. Calibration certificates provide a comprehensive record of the tool's performance, detailing corrections applied and the resulting accuracy.
Zeroing and Reference Points: Establishing a zero or reference point is a deliberate act with profound implications for subsequent measurements. Advanced sensors and electronic components enable precise zeroing, minimizing hysteresis and drift. Users are trained not only to initialize the tool but also to understand the intricacies of zero-setting in different measurement scenarios. This level of sophistication ensures that the reference point is not merely a starting position but a dynamically optimized state for accurate measurements.
Fine Adjustment Features: The inclusion of fine adjustment mechanisms is an engineering feat that involves micro-machining and nanotechnology principles. These features go beyond basic tolerance adjustments; they enable users to make minute changes with micron-level precision. Each fine adjustment mechanism undergoes rigorous testing to ensure its reliability and repeatability. The result is not just a tool with adjustable settings; it is an instrument that empowers users to achieve sub-micron accuracy in their measurements.
Consistent Pressure Application: The requirement for consistent pressure application is not arbitrary but a calculated design choice. Advanced force sensors and feedback systems are integrated to ensure that users apply a consistent force during measurements. This involves the implementation of load cells, strain gauges, and real-time feedback mechanisms. The result is not just a guideline for users but a dynamic control system that optimizes measurements under varying force conditions, contributing to unparalleled precision and repeatability.
Maintenance: Maintenance protocols extend beyond routine care; they involve predictive and preventive measures. Each manual measuring tool is designed with modular components, facilitating easy disassembly. Advanced diagnostic tools, such as laser interferometers and wear analysis systems, are employed during maintenance. Lubrication is not a generic process but a tailored application of specialized lubricants based on wear patterns. The goal is not just tool preservation but predictive maintenance that identifies potential issues before they impact accuracy.
JN27-K Digital Measuring wheel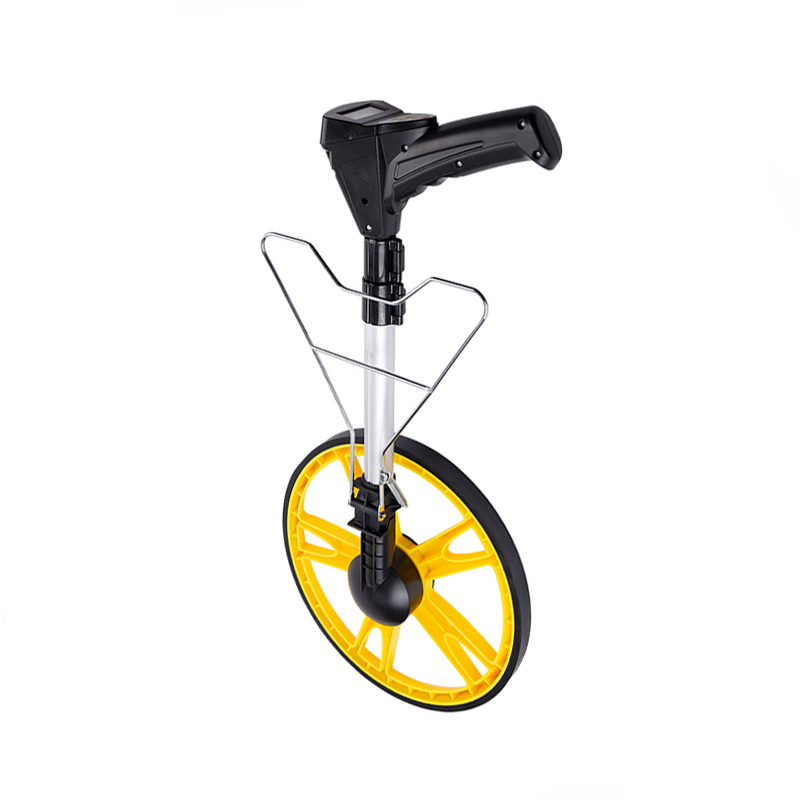