Jaw Design: Digital calipers boast an array of jaw designs engineered to tackle diverse surface textures encountered in various applications. Serrated jaws feature finely machined teeth that securely grip uneven surfaces, preventing slippage and ensuring consistent contact. Wider jaw configurations accommodate larger irregularities, maintaining stability and accuracy. Some advanced models integrate adjustable jaw tension mechanisms, allowing users to tailor grip strength to the surface texture for optimal performance. Specialized coatings or materials, such as carbide or ceramic, enhance durability and friction resistance, further refining the caliper's ability to handle rough surfaces with precision.
Material and Build Quality: The hallmark of professional-grade digital calipers lies in their superior material selection and meticulous construction. These instruments typically employ high-grade stainless steel alloys, meticulously heat-treated and precision-machined to exacting standards. This construction ensures exceptional durability, corrosion resistance, and longevity, even when subjected to harsh working environments and rough surfaces. Advanced manufacturing techniques, such as laser etching and CNC machining, yield ultra-smooth surfaces and tight tolerances, facilitating accurate measurements on irregular surfaces. Some models integrate reinforced components, such as hardened jaws and reinforced frames, to withstand the rigors of heavy-duty use and maintain measurement integrity over time.
Measurement Technique: Professionals rely on refined measurement techniques to mitigate the influence of surface irregularities on accuracy. Employing a systematic approach, users strategically position the caliper jaws to encompass multiple surface features, capturing an average measurement that accounts for variations. Precision pressure application ensures consistent contact with the surface, minimizing errors induced by fluctuations in grip force. Maintaining a perpendicular orientation to the surface plane reduces the risk of angular distortion, preserving measurement integrity. Advanced users may leverage supplementary tools, such as surface probes or depth stops, to further enhance measurement stability and precision on rough surfaces, ensuring adherence to stringent quality standards and specifications.
Stability: Stability is paramount in achieving reliable measurements on rough surfaces, necessitating robust frame construction and smooth, precise movement mechanisms. Digital calipers engineered for professional use feature rigid frames composed of high-strength materials, meticulously engineered to resist flexing and vibration-induced inaccuracies. Integrated linear bearing systems ensure smooth and controlled movement along the measurement scale, minimizing oscillations and transient errors. Advanced models may incorporate dampening systems or anti-backlash mechanisms to further enhance stability and dampen vibrations, ensuring consistent measurement accuracy across diverse surface textures and environments.
Zero Reset Function: The zero reset function empowers users to establish a custom reference point anywhere along the measurement scale, effectively compensating for surface irregularities and enhancing measurement accuracy. Professional-grade digital calipers feature intuitive zeroing mechanisms, allowing users to effortlessly reset the measurement display to their desired starting position with precision and repeatability. This capability enables users to isolate and quantify deviations from the established reference point, facilitating precise measurements of surface features and dimensions. Some advanced models offer customizable zero offset settings and memory functions, enabling users to store and recall multiple reference points for streamlined workflow efficiency and enhanced measurement versatility.
High Accuracy Digital caliper
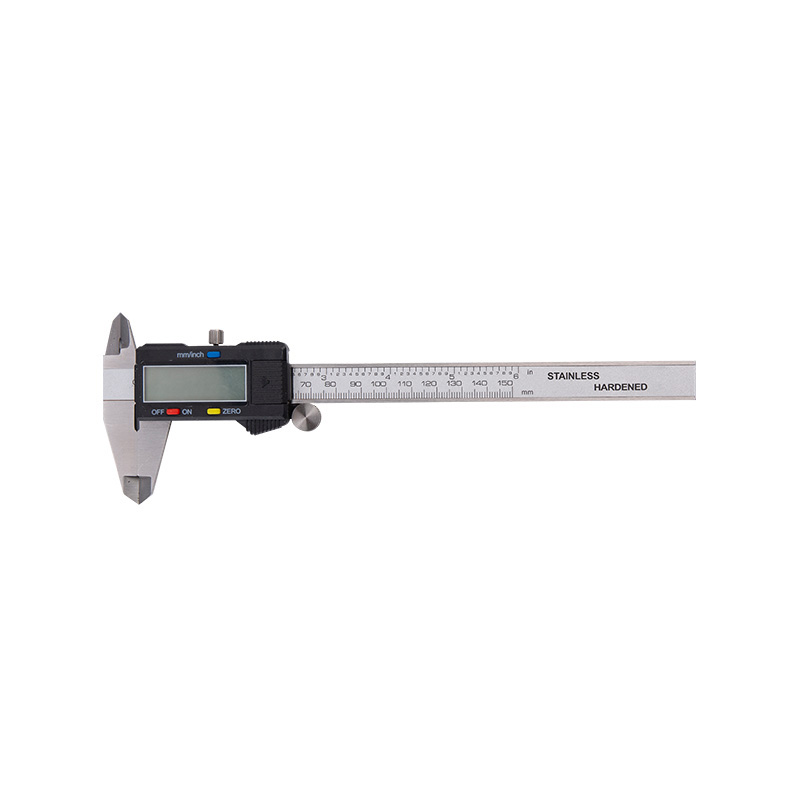